The rise of fast fashion has brought mass production and disposal issues. This has led the apparel industry to face numerous problems, such as water pollution and energy consumption. Questioning this approach, an Okinawan company has taken the opposite path, which has caught the attention of numerous major companies. This story begins with Okinawa’s main agricultural crop, bagasse, the byproduct of sugarcane.
The birth of a new fabric material
Using the “Okinawan treasure”
“SHIMA DENIM WORKS” is located in the corner of the Harbor Town Foreigners’ Housing Complex, an area lined with retro concrete bungalows. Inside the shop are various products, including jeans and kariyushi shirts (Okinawan aloha shirts), certified and produced in Okinawa, and products made from upcycled bagasse. Founder Naoto Yamamoto worked for a Tokyo advertising agency for 17 years before establishing a regional revitalization consulting company and launching the bagasse upcycling project “SHIMA DENIM” in Okinawa.
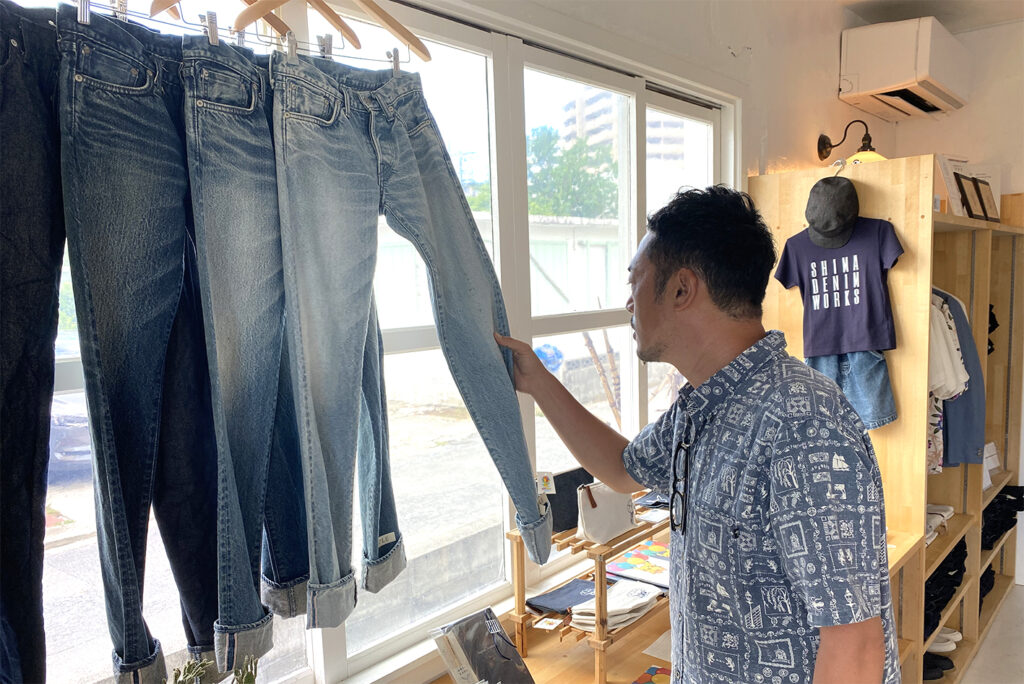
The origin of SHIMA DENIM dates back to Yamamoto’s days in advertising. He visited a sugarcane processing plant through an acquaintance’s introduction, which inspired him.
“At the entrance of the factory, there was a sign that read ‘Sugarcane is Okinawa’s treasure.’ Next to it, there were piles of bagasse, the residue from squeezing sugarcane. When I asked the workers, they mentioned that while some of it was used as fuel for boilers, fertilizer, and animal feed, most was discarded. Despite being called a treasure, it seemed wasteful. I thought there must be a way to utilize it.”
After researching bagasse and meeting acquaintances, Yamamoto saw the potential for bagasse as an “underutilized resource.” The cotton materials we typically wear, or the paper we casually use derives from plants such as cotton and wood. The main component of these materials is cellulose (plant fibers), which is also abundantly present in bagasse.
Yamamoto decided to use bagasse to manufacture and sell jeans made entirely in Japan, from spinning and dyeing to sewing.
“I chose denim because I believe that denim jeans are the only sustainable apparel item from the perspective of maximizing product lifespan. It is said that the production of clothing travels around the Earth 1.6 times, starting from the harvest of raw materials in low-wage countries to the finished product. This production cycle emits carbon dioxide. I wanted to change this situation and create new values for apparel.”
As the first step in denim production, Yamamoto applied for the “Deep Tech Startup Support Program” of the New Energy and Industrial Technology Development Organization (NEDO). NEDO is an organization that supports research and development-oriented startups. After successfully passing the screening process, he obtained a research contract and grant and immersed himself in yarn production using bagasse. Through trial and error with various materials and bagasse blending ratios, it took a year and a half from conception to completion.
Advancing from the Startup Program
Empathy Pushing the Business Forward
While spinning yarn and crafting products, Yamamoto was deeply moved by the reliability of Japanese craftsmanship and the artisans’ passion. The spinning of yarn from slitted bagasse was manufactured in three factories in Fukuyama City, Hiroshima Prefecture, known for its top-notch denim production. From dyeing the cotton used as the warp to weaving the fabric, these factories boast a solid reputation for their exceptional skills.
Currently, the artisans dedicated to Yamamoto’s vision oversee the entire process from spinning to weaving, ensuring a production system that minimizes environmental impact. The woven denim fabric is then transported back to Okinawa, where a denim artisan sews it.
Yamamoto proudly asserts, “Bagasse denim not only embodies our ethical values but also offers superior performance. The fabric weighs about half as much as cotton denim, providing a smooth and quick-drying texture, with high levels of deodorizing and antibacterial properties, which we can prove numerically.”
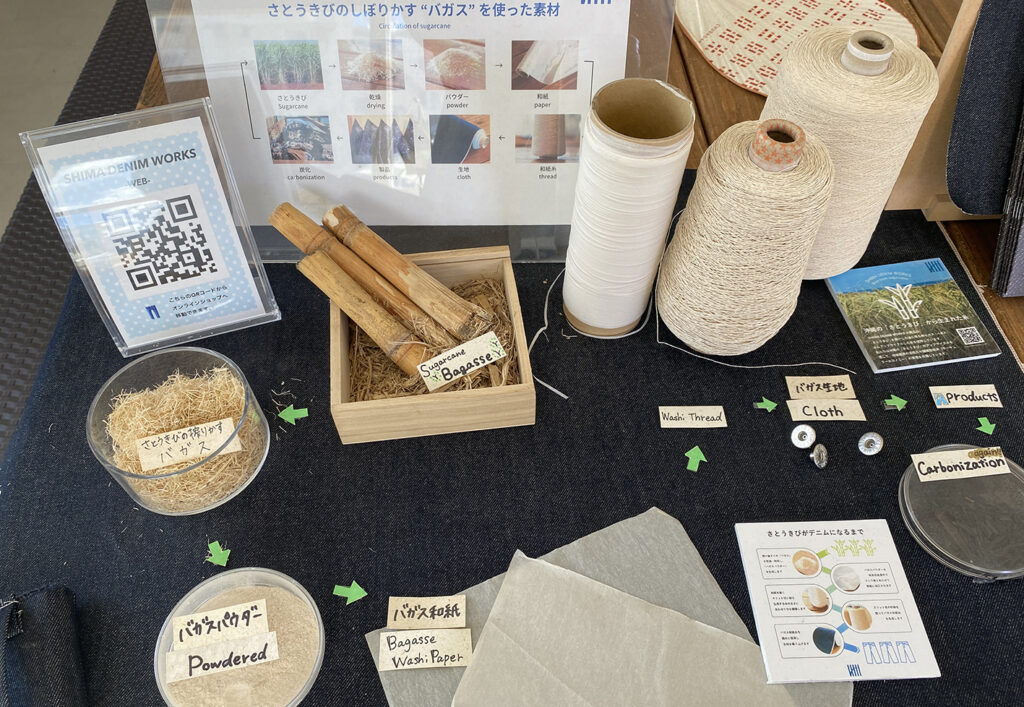
It’s heartening to hear that the residue of crops grown in Okinawa is transformed into a material that suits the hot and humid climate. In 2019, the company obtained patents domestically and in some overseas countries.
The brand’s significant societal importance and name have perked interest from companies. Looking around the store, one can see collaborations with famous anime characters on stationery, and products and posters in partnership with major companies. Despite Yamamoto’s background in advertising, it’s surprising to note that since establishing the store in 2018, SHIMA DENIM WORKS has not run any advertising campaigns.
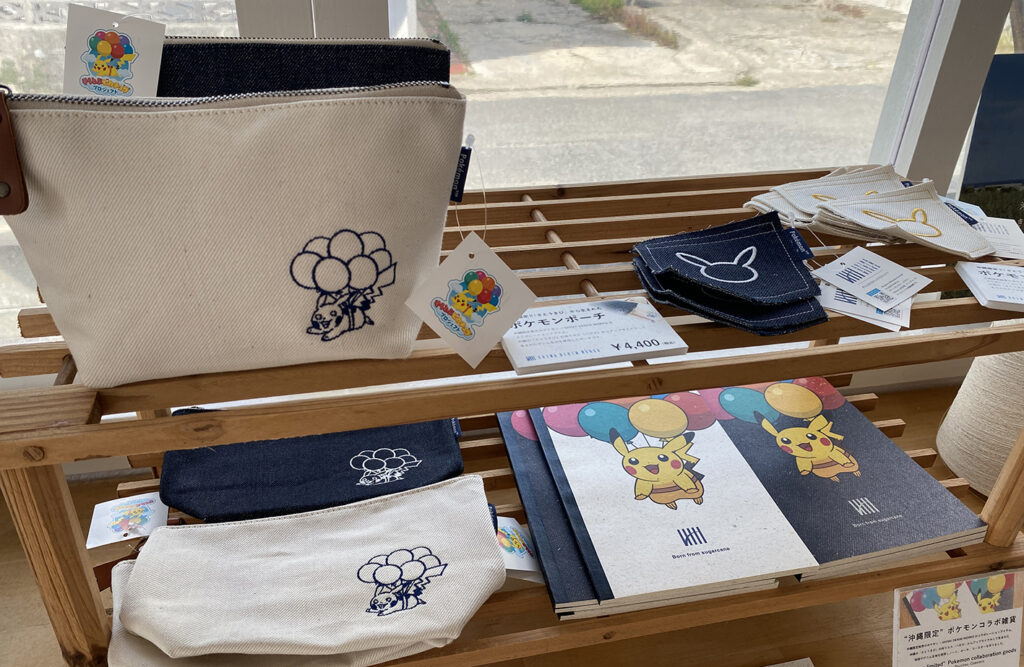
“I didn’t want to make money selling jeans; I wanted people to empathize with the initiative,” says Yamamoto. He often receives inquiries from major companies and local governments wanting to utilize residues from food production such as tea leaves, malt and hops from beer, tomato leaves, cocoa from chocolate, and more.
When asked about the turning point, Yamamoto pointed out that he was selected for the “OKINAWA Startup Program” in 2020, and he received an offer from Japan Transocean Air (JTA), a local airline company based in Okinawa.
“In this program, we were appraised by JTA, and we made konpeito (Japanese sugar candy) containing bagasse for their in-flight sales and karigushi (Okinawan towel) upcycled from seat head covers. Many companies have noticed this initiative, and thanks to that, we have received a lot of inquiries.”
In today’s era, where SDG initiatives have become commonplace in economic activities, SHIMA DENIM’s B-to-B expansion is expected to broaden its reach further.
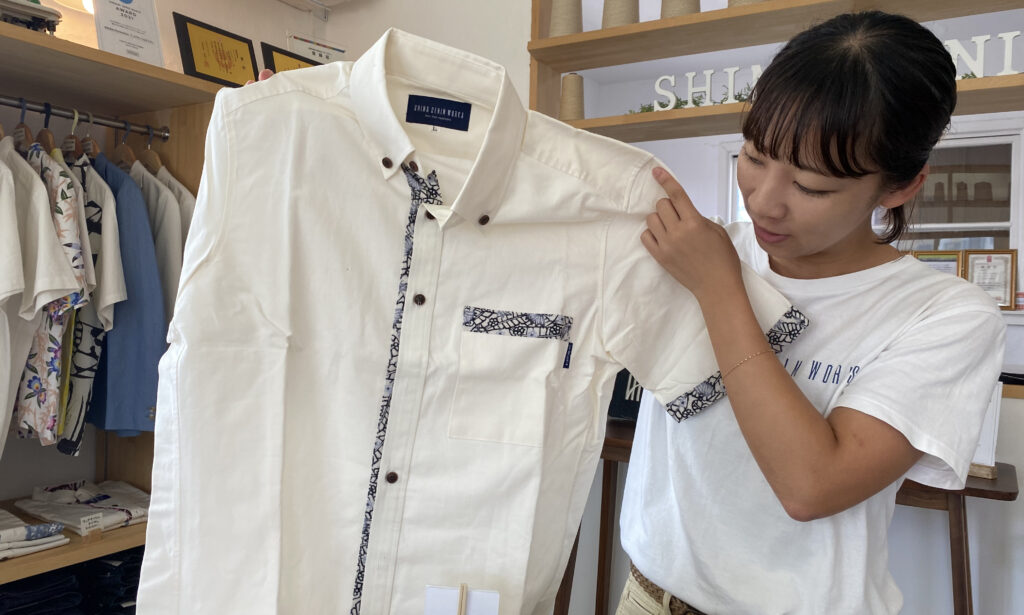
Teaming up with IT companies in Okinawa
Expanding eco-friendly sharing services with IoT
Yamamoto, aiming for waste-free circular manufacturing, is also expanding the sharing service “Bagasse UPCYCLE,” which uses bagasse. This initiative was launched as a joint venture with Okicom, a well-established IT company in Okinawa.
“The proposal is to prevent clothing from being unnecessarily made if it’s only going to be worn once or twice and then stored away. We suggest renting them instead. We aim to extend the product’s lifespan by having many people wear it, and carbonize it for sugarcane fertilizer in the end.”
This rental kariyushi is an IoT-enabled item. By scanning the tag sewn onto the kariyushi with a smartphone, you can see the complete history of its production, including the date and time of spinning, weaving, and details about the factory where it was made. Okicom’s provides the technology for this feature.
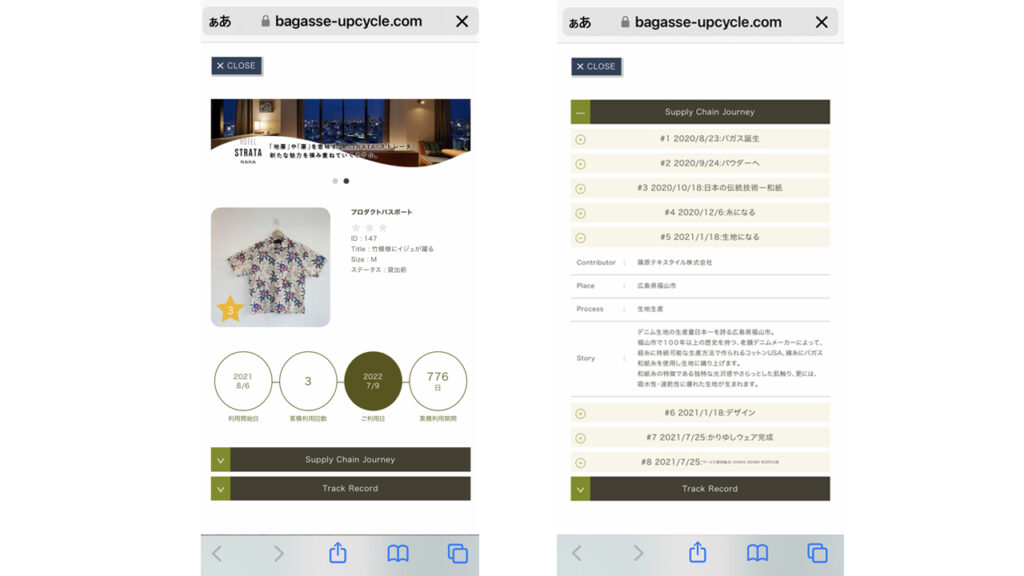
“Many products claim to be environmentally friendly, but there are often without clear traceability. With this system in place, we can effectively communicate that aspect and allow customers to feel connected with the producers, which in turn increases affection for the clothing. Moreover, if we can pique people’s interests, it will lead to more people wearing it and extending the product’s lifespan,” says Yamamoto.
Upcycling from Okinawa
Sending a message to the world
When asked about expanding overseas, he mentioned several projects were already underway. There are plans to transport Thai bagasse to Japan for manufacturing and sell the products in Thailand. However, the ultimate goal is to produce yarn in Thailand. There are also discussions about upcycling products using tea leaf residue from Kenya.
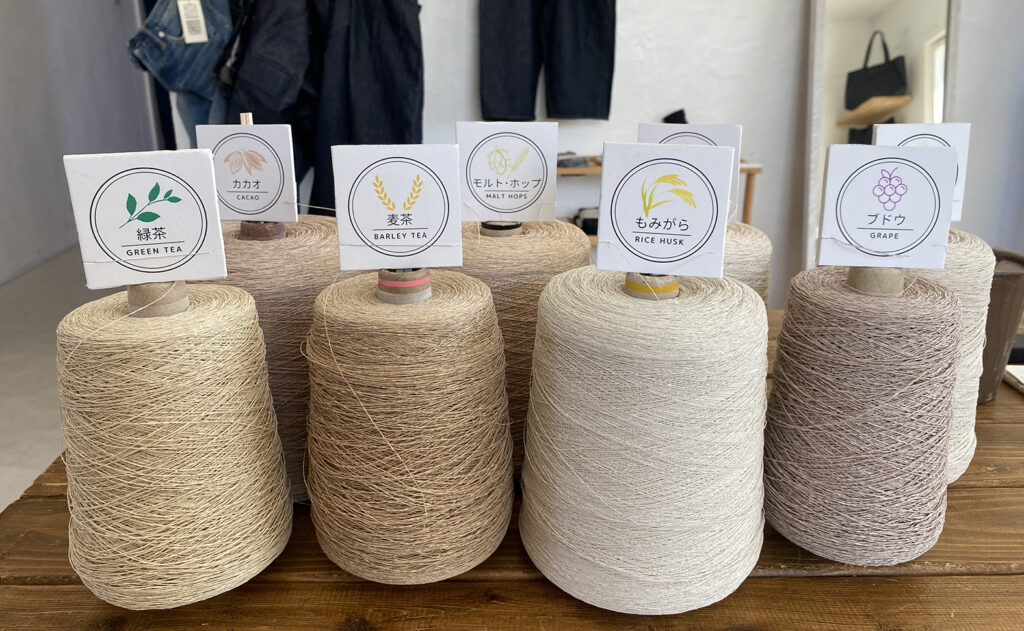
“Our business model revolves around upcycling as much underutilized resources as possible, even just a gram, to build a circular economy. Through this initiative, we aim to discover new value not only domestically but also worldwide. We want to establish and disseminate an upcycling business model originating from Okinawa to the world,” shared Yamamoto.
Yamamoto’s endeavour for a waste-free circular economy to become the norm continues.
Interview and Japanese Text by Minako Narabayashi